The surface quality of the workpiece after slow wire EDM is not only measured by the surface roughness, but also the defects such as the metamorphic layer, so the surface integration is proposed (SI=Surface Integrity, also translated as “surface integrityâ€). concept. In this article, Xia Mier introduces the situation of surface integrated wire cutting by configuring SI (or CC) pulse power supply on its wire cutting machine.
First, what is the new feature to achieve? This was achieved with a new power electronics board that was assembled on the ROBOFIL 1020 series machine that was produced after May 1996. The machine name was changed from ROBOFIL1020 to ROBOFIL1020SI series.
The purpose of this counter electrolysis (AE) power box is to achieve the effect of surface integration (SI = Surface Integrity) for changes in materials during electrical discharge machining.
Second, what is surface integration (or clean cutting - CC = Clean Cut)?
During the electrical discharge machining process, there are many physical phenomena that cause damage or change to the surface of the material, and even destroy. The affected layer can be as deep as 30 μm below the surface layer.
The following major adverse consequences can be found in this affected layer:
Micro-cracking crack
Cobalt depletion cobalt hollowing
Redeposit of wire metal material
Recast of melted cobalt
Water corrosion
The consequences of unconformity of bad surfaces
1. Defective mechanical properties in the affected layer will cause the workpiece material to deteriorate or shorten the life of the die.
2. If the surface of the cemented carbide punch and die is not integrated, the surface will be easily broken and the anti-wear coefficient will be affected, so that the wear will become larger and the die (knife) will have a shorter life.
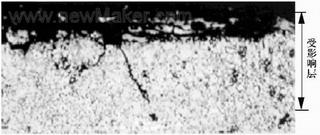
Figure 1 Cemented Carbide: Tungsten Carbide Containing 6% Cobalt Element
3. What physical phenomena can have adverse effects on surface integration? Xiamir Technology has approached the world to define and analyze the various factors that adversely affect the surface integration of the material during electrical discharge machining.
The results are as follows:
·Overheat damage
The thermal effect of the internal temperature rise of the material during discharge, which will lead to local stress and crack generation
·Erosion effect
From a chemical point of view, water is an erosive solvent for any metal.
·With an electrolytic reaction process
When a current passes through a dielectric fluid, it causes some chemical reactions, which adversely affects the material. 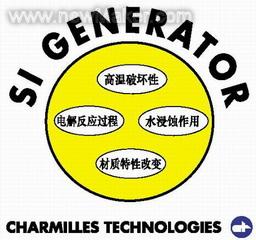
·Material characteristics
Different materials have different degrees of reaction to the intersection of heat, water and electrolysis, especially the alloy materials with mixed components will be more adversely affected.
Each of the above bad physical and chemical phenomena is important and works together and is related to each other. If you just want to seek to reduce the single bad phenomenon to the limit (for example: electrolytic process effects) will not be a reliable solution.
Xiamir Technology has developed this new SI power circuit to provide a solution to this global headache problem.
For the development of material properties, Charmilles and the Swiss carbide manufacturer STELLRAM work together to develop new technologies.
Some AE (counter-electrolytic) power boxes from machine tool builders have only partially solved the problem of an electrode (electrode-chemical reaction), and Xiaer Technology's SI power box provides a complete solution. This power box also achieves the effects of reverse electrolysis and surface integration and provides a wide range of processing technology conditions.
Carbide processing: The affected layer is the result of a combination of various physical and chemical phenomena.
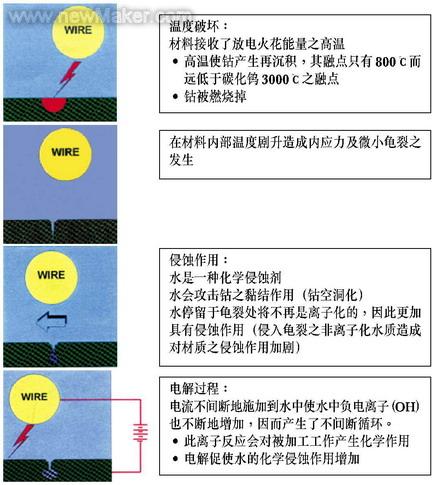
|
|
4. What are the electrical characteristics of the SI power supply circuit?
Discharge energy
The discharge spark contains a large amount of energy to transfer a large amount of heat into the interior of the material, which will generate a large amount of molten metal molecules around the metal removal point, so the internal stress of the material is generated by the interaction of the uninterrupted heat and the cooling water.
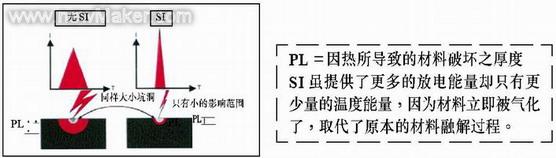
How is the material crack?
Erosion rate
The ratio of the original material removal to the thickness of the affected layer is thus much improved, ie the same result can be obtained with fewer processing steps.
Conversely, the cobalt element (acting as a binder polymerizer in tungsten carbide) is hollowed out by the electrode-chemical attack, and the other elemental crystal grains of tungsten carbide will no longer be substantially solidly bonded together.
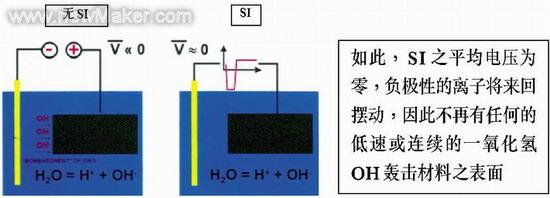
5. What are the performances of SI(CC) power circuits and what are the main features? All electronic boards with effects on SI characteristics have been tested and installed as standard in machine tools.
The SI(CC) power box can be used with a new processing technology condition table. The first work of SI (CC) is the processing of cemented carbide materials.
For all hard alloys processed from a thickness of 0 to 100 mm, the effect of SI can reach a surface roughness of at least Ra 0.25 μm, which is a standard configuration.
6. What are the benefits of SI (CC)?
‧Surface integration effect
Various adverse effects on the surface of the material during discharge spark machining are minimized.
‧Improve surface roughness
It has processing conditions from 0 to 100 mm thick.
‧Processing speed
To achieve the same surface roughness, it can be achieved by reducing the number of processing times, increasing the speed and integrating the surface.
Example of machining cemented carbide with wire diameter 0.25mm
‧ Geometric accuracy improvement
The parallelism (or flatness) of the workpiece is improved. 
|
|
[There are comments, click to view] [Editor:]
Metal processing industry related news
Keywords: wire cutting edm - Characteristics of Suzhou Changfeng Micro-hole Machining Diesel Engine and Gasoline Engine Injector Hole 2010-12
- How to adjust the gap tracking tightness during the cutting process of Suzhou Changfeng Line 2010-11
- Suzhou Changfeng EDM machine wire selection and adjustment 2010-10
- Suzhou Changfeng EDM CNC Wire Cutting 2010-10
- How to adjust the wire and the wire rod in Suzhou Changfeng line cutting 2010-09
- Preparation of fast-cut wire cutting working fluid 2010-09
- 39 cases of wire cutting machine common problems (3) 2010-07
- Understanding the selection of wire cutting machine tools 2010-07
- Cimatron China launches wire cutting Chinese training manual Fikus 2006-05
- Create a world famous brand that belongs to China 2006-05
How do you feel after reading “ Surface Integrated Wire Cutting �
User Comments: Surface integrated wire cutting
There are comments, click to view Guess what products and companies you like
Function changeLink(){ window.location.href= window.location.href+'#top'; } all rights reserved

Machinery Industry Information Institute
 Metal processing online MW1950 copyright ©2006-2012 mw1950.com .All Rights Reserved BAIDU_CLB_SLOT_ID = "398230"; var _bdhmProtocol = (("https:" == document.location.protocol) ? " https://" : " http://"); document.write(unescape("%3Cscript src= '" + _bdhmProtocol + "hm.baidu.com/h.js%3Fed9eb0e17f50c86a478c357e7243dac7' type='text/javascript'%3E%3C/script%3E"));
Function scrollx(p){ var d = document,dd = d.documentElement,db = d.body,w = window,o = d.getElementById(p.id),ie6 = /msie 6/i.test(navigator. userAgent),style,timer; if(o){ o.style.cssText +=";position:"+(pf&&!ie6?'fixed':'absolute')+";"+(pl==undefined?' Right:0;':'left:'+p.l+'px;')+(pt!=undefined?'top:'+p.t+'px':'bottom:0'); if(pf&&ie6){ o.style.cssText +=';left:expression(documentElement.scrollLeft + '+(pl==undefined?dd.clientWidth-o.offsetWidth:pl)+' + "px");top:expression(documentElement.scrollTop +'+(pt==undefined?dd.clientHeight-o.offsetHeight:pt)+'+ "px" );'; dd.style.cssText +=';background-image: url(about:blank);background -attachment:fixed;'; }else{ if(!pf){ w.onresize = w.onscroll = function(){ clearInterval(timer); timer = setInterval(function(){ // double select in order to fix chrome under xhtml When parsing, dd.scrollTop is 0 var st = (dd.scrollTop||db.scrollTop),c; c = st - o.offsetTop + (pt!=undefined?pt:(w.innerHeight||dd.clientHeight)- o.offsetHeight); if(c!=0){ o.style.top = o.offsetTop + Math.ceil(Math.abs(c)/10)*(c<0?-1:1) + 'px'; }else{ clearInterval(timer); } },10) } } } } } /* id The id of the content you want to scroll l The position of the abscissa is not written as close to the right t. The position you want to place on the page is by default with the bottom edge 0 is attached to the top edge f 1 to indicate that the top is not written or 0 is scrolling * / scrollx({ id:'bb', l:20, t:490, f:1 }) $(document).ready(function(){ if($("a").attr('target')=='_self'){ $("a").attr('target',"_blank") ; } if($("a").attr('rev')!=''){ $("a").attr('target',"_blank"); } }); function AddToFavorite() { If (document.all){ window.external.addFavorite(document.URL,document.title); }else if (window.sidebar){ window.sidebar.addPanel(document.title, document.URL, ""); } //=Click to expand and close the effect = function openShutManager(oSourceObj,oTargetObj,shutAble,oOpenTip,oShutTip){ var sourceObj = typeof oSourceObj == "string" ? document.getElementById(oSourceObj) : oSourceObj; var targetObj = typeof oTargetObj == "string" ? document.getElementById(oTargetObj) : oTargetObj; var openTip = oOpenTip || ""; var shutTip = oShutTip || ""; if(targetObj.style.display!="none"){ if(shutAble) return ; targetObj.style.display="none"; if(openTip && shutTip){ sourceObj.innerHTML = shutTip; } } else { targetObj.style.display="block"; if(openTip && shutTip){ sourceObj.innerHTML = openTip ; } } } function views(){// var views = getcookie('views'); if(views>4){ } } function soso_fuc(){ var offset = $('#soso1').offset(); $("#soso").css('left' ,(offset.left+2)+"px"); $("#soso").css('top',(offset.top+33)+"px"); $("#soso").css ('display',''); $("#jiao_img").attr("src",'../../style/duihao/images/infor_show_jiao2.gif'); } function soso_click(type_valye,soso_type_id) { $('#type').val(type_valye); $('#soso2').html($('#'+soso_type_id).html()); $('#soso').css('display ','none'); $("#jiao_img").attr("src",'../../style/duihao/images/infor_show_jiao.gif'); } function add_out(){ if($( "#hidden_div").val()==0){ $('#soso').css("display","none"); $("#jiao_img").attr("src",'.. /../style/duihao/images/infor_show_jiao.gif'); } } function hidden_div(){//type=1 displays the status, when 0 is hidden $("#hidden_div").val(1); } function block_div(){//type=1 displays the state, 0 is hidden $("#hidden_div").val(0); } document.body.oncopy = function () { setTimeout( function () { Var text = clipboardData.getData("text"); if (text) { text = te Xt + " This article is from "Metal Processing Online" Reprinted please indicate the source URL in the form of a link: "+location.href; clipboardData.setData("text", text); } }, 100 ) }
Ball Valves
There are five general body styles of ball Valves: single body, three-piece body, split body, top entry, and welded. The difference is based on how the pieces of the valve-especially the casing that contains the ball itself-are manufactured and assembled. The valve operation is the same in each case.
In addition, there are different styles related to the bore of the ball mechanism itself.
Ball valves in sizes up to 2 inch generally come in single piece, two or three piece designs. One piece ball valves are almost always reduced bore, are relatively inexpensive and generally are throw-away. Two piece ball valves are generally slightly reduced (or standard) bore, they can be either throw-away or repairable. The 3 piece design allows for the center part of the valve containing the ball, stem & seats to be easily removed from the pipeline. This facilitates efficient cleaning of deposited sediments, replacement of seats and gland packings, polishing out of small scratches on the ball, all this without removing the pipes from the valve body. The design concept of a three piece valve is for it to be repairable.
Stainless Steel Ball Valves, Brass Ball Valves, Sanitary Ball Valves, Water Ball Valves
ZHEJIANG KINGSIR VALVE CO., LTD. , https://www.kingsir-valve.com